- 10 Facts Regarding Laser Welding Technology
- Advantages of Laser Welding
- Common Faults And Solutions for Laser Welding
- The development history of laser welding technology
- Applications of laser welding technology
- Future Trends in Laser Welding
- 1. Intelligent Development
- 2. Green and Environmental Protection
- 3. Various Applications
- 4. Technological Innovation And Efficiency Enhancement
- 5. Extension of Application Fields
- 6. Market Demand Increase
- 7. Integrating Automation And Intelligence
- 8. Customization And Personalized Production
- 9. Development of Home Lasers
- 10. Talent Development And Technological Innovation
- In Conclusion
As one of the key technologies in modern manufacturing, laser welding has broad application prospects and important economic value. With the continuous advancement of science and technology, laser welding technology is increasingly widely used in various fields, from automobile manufacturing to electronics, and then to all aspects of manufacturing, which are inseparable from the support of laser welding technology.
This article aims to deeply explore the ten truths of laser welding technology, including its applicable materials, micro-welding capabilities, large weld welding capabilities, result repeatability, precise controllability, speed advantages, low heat input, fewer component size restrictions, easy integration with motion products, and cost-effectiveness. At the same time, it will also analyze the advantages of laser welding technology, such as high power density, fast welding speed and high quality, welding under special conditions, micro-welding, great flexibility, and high system flexibility. In addition, the article will also introduce the common defects and solutions of laser welding, the development history of laser welding technology, application fields and future trends.
Through a comprehensive analysis of laser welding technology, it is hoped that readers will have an opportunity to gain a deeper understanding of laser welding technology and provide a reference for research and application in related fields. At the same time, it is also hoped that it will promote the continuous innovation and development of laser welding technology and contribute to the advancement of modern manufacturing.

10 Facts Regarding Laser Welding Technology
1. Suitable for A Variety of Materials
Laser welding technology has a wide range of material applications and can link a variety of metals, including stainless steel, nickel, titanium, inconel, and molybdenum. Laser welding, in particular, can easily handle reflective materials like copper and aluminum, which would be difficult, if not impossible, to connect with traditional welding techniques.
2. Microwelding Is Conceivable
Laser welding is an important process in the welding of medical device components. Laser welding is becoming the ideal procedure for small items like microfluidic chips and surgical equipment, as well as welding in hard-to-reach areas. It is capable of high-precision welding, ensuring the equipment’s performance and reliability.
3. Large Welds Can Be Produced
Laser welding is capable of welding thicker materials as well as micro welding. It can produce structural welds up to 1/2 inch deep to fulfill the welding requirements of materials of varying thicknesses. Laser welding, for example, can be used to create high-strength connections in the manufacturing of some major industrial equipment.
4. Highly Repeatable Outcomes
The outcomes of laser welded components are extremely repeatable. Once the suitable welding parameters have been found, welding can be repeated in the same manner to ensure uniform quality in each weld joint. This is crucial for large-scale production and industries that require high-quality welding.
5. Precise And Controlled
Laser welding is a non-contact procedure that allows for exact control over the size of the laser beam, which in turn controls the size of the heat-affected zone. This increases welding precision, minimizes thermal damage to surrounding materials, and enhances welding quality. At the same time, the range of the heat-affected zone can be flexibly modified to meet various welding requirements.
6. Unmatched Speed
Laser welding is far faster than traditional TIG welding. TIG welding takes hours to complete, whereas laser welding takes only a few minutes. The laser can travel at speeds of hundreds to thousands of millimeters per minute, significantly increasing production efficiency.
7. Low Heat Input
Laser welding transfers heat in a narrow, controlled area, requiring less heat input than other welding methods like MIG welding. This reduces residual stress on the component, preserves more metallurgical structures, and improves welding quality. At the same time, laser welding can control the heat-affected zone, preventing damage to heat-sensitive internal components.
8. Minimal Limits On Component Size
Laser welding can be done in open air or in a glove box, with fewer constraints on component size. With a strong laser, you can process larger components. This simplifies the production of massive industrial equipment.
9. Simple Integration with Motion Goods
Laser welding is easily compatible with off-the-shelf motion devices such as CNC platforms and robots. Robots have been employed for welding since 1962, and their applications are growing increasingly diverse. The route to innovation in this technology has already been laid, and it is becoming increasingly sophisticated. The combination of laser welding and robots allows for flexible automated welding, which improves production efficiency and welding quality.
10. Cost-effective
Laser welding is quick, controllable, and repeatable, making it incredibly productive and efficient. Although the initial investment in laser welding equipment may be considerable, it can result in significant time and cost savings in the long run. High-quality welding outcomes are achieved without losing budget, making it a cost-effective welding procedure.
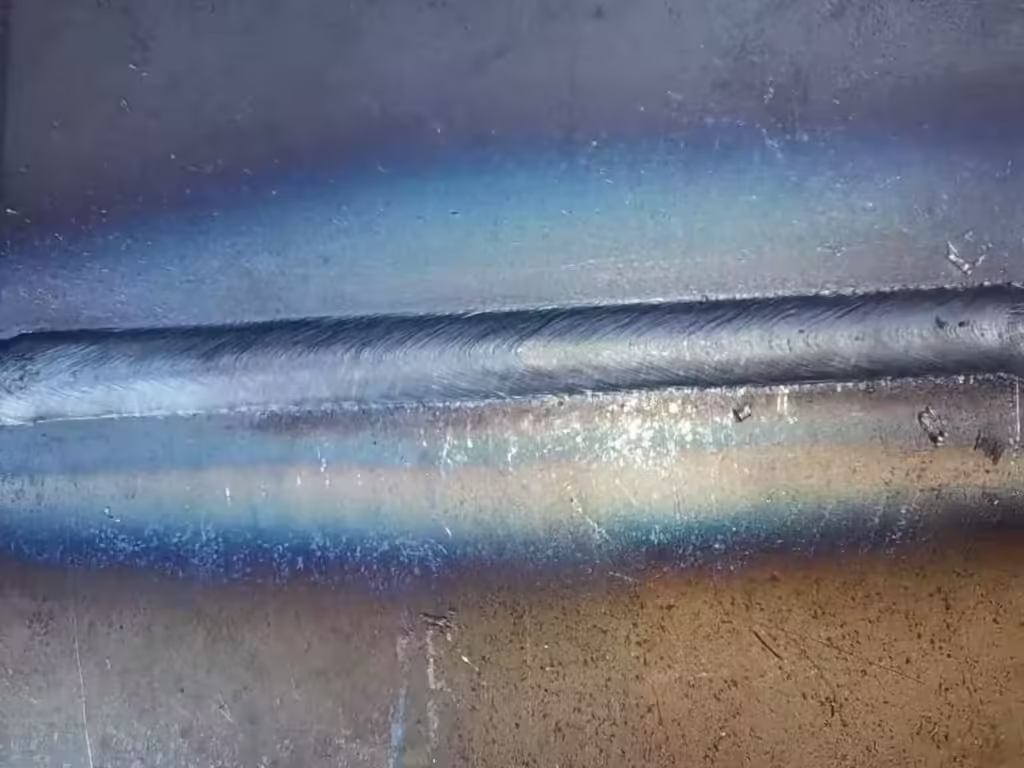
Advantages of Laser Welding
1. High Power Density
Laser focusing results in a power density of 106-108W/cm², well above the arc’s value. This high power density allows the metal material to quickly heat up to the melting point during laser welding, resulting in faster welding. At the same time, increased power density provides the benefits of greater depth and less distortion. During the welding process, laser energy is delivered to the deep part of the workpiece via the small hole, resulting in reduced lateral diffusion and a bigger area welded per unit time, hence boosting welding efficiency.
2. Quick Welding with Good Quality
Laser welding speeds are several times, if not dozens, faster than traditional welding procedures. Laser welding’s low heat input results in a tiny heat-affected zone and minimal post-welding grinding. This is a significant advantage for some factories that want to increase output. The heat output is stable, particularly for thin plates (stainless steel), which can reduce rework, increase production efficiency, and lower costs. Furthermore, laser welding can increase welding quality and aesthetics, resulting in a smoother and more beautiful weld.
3. Ability to Weld under Specific Situations
Laser welding can be done at ambient temperature or in controlled settings, and the welding equipment is simple. For example, when the laser travels through an electromagnetic field, the beam does not deviate; the laser can weld in a vacuum, air, or a specific gas environment, as well as through glass or beam-transparent materials. This property makes laser welding excellent for welding a variety of unique materials, including refractory materials such as titanium and quartz, as well as weld heterogeneous materials with satisfactory results.
4. Capability to Execute Micro Welding
After concentrating, the laser beam can produce a very small spot, as small as 0.1mm, which can be precisely positioned. This makes laser welding suitable for the assembly welding of micro and small workpieces in large-scale automated production. Laser welding, for example, can be used in electronic assembly to connect microscopic components in an efficient and exact manner, enhancing manufacturing efficiency and product quality.
5. High Flexibility
Laser welding can weld inaccessible locations, perform non-contact long-distance welding, and is extremely flexible. The use of fiber transmission technology in YAG laser processing technology, as well as the popularization of fiber continuous lasers, have increased the popularity and use of laser welding technology, making it easier to automate and integrate. For example, laser welding can easily weld hard-to-reach sections on workpieces with complex shapes.
6. High System Flexibility
The laser welding technique is extremely adaptable and easy to automate. Computer programs can manage the welding process, allowing for exact parameter adjustments and automated operation. For example, automated laser welding technology in the automotive industry can significantly improve production efficiency and product quality. At the same time, the laser welding system can be combined with other equipment to provide multi-station processing, which allows for more precise welding.

Common Faults And Solutions for Laser Welding
1. Welding Spatters
Welding spatter is a common issue during laser welding. The major reason is that the surface of the processed material or workpiece has not been cleaned, there are oil stains or contaminants present, or the galvanized coating has volatilized. In addition, splatter is directly proportional to power density. To reduce spatter, before to laser welding, the material or workpiece should be thoroughly cleaned to ensure that no contaminants are present on the surface. On the other hand, lowering the welding energy can effectively reduce the production of spatter.
2. Cracks
Continuous laser welding produces thermal fractures, including crystallization and liquefaction cracks. The fundamental cause of the cracks is that the weld generates a large contraction force before it entirely solidifies. Wire filling, preheating, and other methods can help reduce or eliminate cracks. High-frequency pulses or filling metals can reduce segregation time and the occurrence of liquefaction cracks.
3. Porosity
Laser welding is more likely to produce porous materials. One explanation is because the laser welding molten pool is deep and narrow, and the cooling rate is extremely fast, giving the gas created in the liquid molten pool insufficient time to escape. Second, the weld surface is not cleaned, and the zinc vapor from the galvanized sheet evaporates. The answer is to clean the workpiece and weld surfaces before to welding to improve zinc volatilization when heated. At the same time, the blowing direction will influence the production of pores, thus it should be regulated appropriately.
4. Undercut
The main reasons for undercut are that the welding speed is too fast, resulting in the liquid metal in the weld not being redistributed on the back of the small hole, forming undercuts on both sides of the weld; the joint assembly gap is too large, the molten metal in the joint filling is reduced, and undercuts are also prone to occur; at the end of laser welding, if the energy drop time is too fast, the small hole is easy to collapse, causing local undercuts. The solution is to adjust the laser welding machine’s processing power and speed to match and prevent undercuts. Weld undercuts discovered during the inspection can be polished, cleaned, and repaired to satisfy the acceptance standards.
5. Weld Accumulation
Weld buildup occurs when the wire feeding speed is too high or the welding pace is too sluggish. The answer is to raise the welding speed, decrease the wire feeding speed, or reduce the laser intensity to ensure that the weld is filled appropriately and not too high.
6. Welding deviation
Welding deviation is caused by incorrect positioning during welding, incorrect filling welding time, and welding wire alignment. The welding deviation problem can be efficiently solved by modifying the welding position, welding time, welding wire position, and the position of the lamp, welding wire, and weld.
7. Weld Depression
The weld depression is created by a poor center of the weld during brazing; the center of the light spot is close to the lower plate and deviates from the center of the weld, melting some of the parent material. Adjusting the light wire matching is the primary way for resolving weld depression.
8. Poor Weld Formation
Poor weld formation is caused by unsteady wire feeding or discontinuous illumination during the weld brazing process. Adjusting the equipment’s stability to guarantee consistent wire feeding and light can help with poor weld formation.
9. Uneven Weld Bead
Uneven weld beads are caused by substantial changes in weld trajectory and uneven training. Welding with the best conditions, changing the viewing angle, and making the corners coherent will effectively prevent uneven weld bead.
10. Surface Slag Inclusion
Surface slag inclusion can be caused by an unclean interlayer coating during multi-pass welding, an uneven surface of the preceding weld or a weldment surface that does not satisfy the criteria, and incorrect welding operation techniques such as low welding input energy and excessive welding speed. The solution is to choose an appropriate welding current and speed. During multi-pass welding, the interlayer coating must be thoroughly cleaned. Grinding can be used to remove surface slag from welds, and repair welding can be conducted as needed.

The development history of laser welding technology
1. Research start-up Stage
Laser welding was still in its early stages of development throughout the 1960s and 1970s. During this time, scientists began to boldly investigate the idea of employing laser beams for welding, conducting a series of trials and study. However, due to the immaturity of laser technology at the time, various issues arose, including insufficient laser stability and difficulty correctly managing energy output. These variables created significant hurdles in the practical application of laser welding, which was not feasible enough. Despite this, scientists refused to give up. They continued to commit a significant amount of time and energy, building the groundwork for the future development of laser welding technology.
2. Commercialization Stage
From the 1980s to the 1990s, laser welding entered the commercial phase. The commercial application of laser welding has continuously risen as laser technology continues to improve and mature. Laser welding is currently widely employed in a variety of major industries, including vehicle manufacture, electronic equipment manufacturing, aerospace, and so on. For example, German automakers Audi, Mercedes-Benz, and Volkswagen were among the first to adopt laser welding for sheet metal welding on roofs, bodies, and side frames. In the United States, General Motors, Ford, and Chrysler fought to integrate laser welding into automotive manufacturing. Although they started later, they grew quickly. Fiat of Italy employs laser welding to assemble most steel plate components, and Nissan, Honda, and Toyota Motor Corporation of Japan use laser welding technology to make body panels. According to data, high-strength steel laser welding assemblies are becoming more popular in automotive body welding due to their superior performance. Laser welding is crucial in the creation of microelectronic devices because of its great precision and low thermal impact. The aerospace industry has extremely high welding quality standards, and laser welding may meet those standards for high strength and precise welding.
3. Further Growth Stage
Laser welding has advanced significantly since the 2000s. Laser welding efficiency and precision have improved over time as science and technology have advanced. The introduction of new technologies such as short-pulse laser welding and laser hybrid welding has broadened the application area of laser welding. Short-pulse laser welding, for example, produces high-energy laser pulses in a very short period of time, allowing for high-precision welding of microscopic components. Laser hybrid welding combines the benefits of many welding processes and may accommodate more complex welding requirements. Laser welding is also employed in the manufacture of precision instruments and microelectronic devices. In these applications, laser welding’s excellent precision and low heat-affected zone are completely utilized. At the same time, with ongoing advances and innovations in laser technology, laser welding is becoming increasingly crucial in modern manufacturing. According to relevant statistics, the sales revenue of China’s laser welding equipment market in 2023 was around 11.52 billion yuan, a 38.6% growth over the previous year, demonstrating the critical role and extensive development prospects of laser welding technology in modern manufacturing.
Applications of laser welding technology
1. Automobile Manufacturing Sector
Laser welding technology is extremely important in the automotive industry. Laser welding can be used in automobile body manufacturing to laser weld plates of varying thicknesses, connect plates of varying thicknesses and materials into a whole, increase plate utilization from 40% – 60% of traditional processes to 70% – 80%, reduce body weight, and improve the overall mechanical properties of the structure. Laser welding of body assemblies and sub-assemblies, such as the attachment of the top cover to the side panel, side panel welding, and door welding, is becoming more common. Some models, including Ford SUVs and sedans, as well as many Volkswagen models, use laser self-melting welding for the side panels. Volvo continues to use laser self-melting welding for body welding, primarily for connecting the top cover to the side panel, welding the side panel, and welding the door. Laser welding of automotive parts, such as gears and transmissions, is also quite prevalent.
The use of laser welding in automobile manufacturing can not only lower the weight of the car body, which saves fuel, but it can also improve assembly precision, stiffness, and therefore safety. For example, the use of laser welding machines in automobile manufacturing has greatly improved the precision of the car body structure, and dynamic and static rigidity can be increased by more than 50% when compared to other welding processes, reducing noise and vibration while driving, improving ride comfort, and improving the car’s safety performance. The use of unequal thickness laser welded plates in automobile manufacturing can reduce the weight of the car body, reduce the number of parts, improve safety and reliability, and reduce production costs; in terms of body welding, it is widely used in the assembly and connection of body stamping parts, including laser welding of roof covers, trunk covers, and frames; another important application of body laser welding is laser welding of The car seat laser welding workstation is primarily used for laser welding the front, middle, and rear backrests, sliding rails, height adjusters, and angle adjusters of vehicle seats. It has several advantages, including high welding efficiency, minor deformation, high precision, and lightweight. The completely autonomous laser welding system is capable of welding numerous steel plates of varying thickness, strength, and material into a stampable plate. It has been effectively utilized to weld automotive elements such as body pillars, door inner panels, side panels, front longitudinal beams, and sunroofs. The laser welding workstation for vehicle transmission components can be tailored based on the welding products, allowing for multi-station quick welding and processing changeover of different workpieces.
2. Electronic Field
Laser welding is a popular technology in the electronics industry. Laser welding is used in the microelectronics industry to manufacture integrated circuit boards and electronic components because it has low thermal efficiency and provides concentrated and quick heating, making it a key part of the integrated circuit and semiconductor device packaging process. For example, in the electronics industry, tin-based alloy filler metals are now used for welding to complete device packing and card assembly. Wave soldering and reflow soldering are traditional soldering methods, but they pollute the environment, whereas laser soldering does not, and it is ideal for small, thin, and vertical welding applications. Laser soldering machines are used in the majority of precision digital electronics sectors, including headphones, semiconductors, communications, vehicles, fuses, wire electrical devices, CCM modules, and FPC/PCB/FCP boards.
The VCM component in the camera module has a small solder joint size, and traditional soldering is powerless, whereas laser soldering has a minimum spot size of 50 microns or even lower, making it an advanced soldering method for precision parts similar to VCM components. Solder paste laser welding is commonly used for part reinforcement or pre-tinning, and it provides excellent welding results on camera modules and VCM voice coil motors. Laser welding technique has also demonstrated distinct advantages in the sector of battery manufacture. For example, in battery tab welding, by precisely adjusting the laser parameters, the tab and the battery pole can be precisely connected in a very short time, improving the stability and safety of the welding joint; in button battery welding, by finely controlling the laser energy and welding speed, the consistency of the product is improved, potential battery damage is reduced, and battery life is extended. In addition, miniaturized welding of integrated circuit boards necessitates exceptional precision. Laser welding technique can reach micron-level precision welding, which matches the stringent precision requirements of integrated circuit boards while also improving welding quality and dependability. Laser welding technique offers a high-sealing and high-reliability packaging solution for precision sensors, protecting them from physical damage and environmental influences. Consumer electronic items, such as cellphones, have complicated internal systems and expanding capabilities. Laser welding can more efficiently assure a flawless connection between parts, reducing quality issues with mobile phones caused by part breakage.
3. Manufacturing Field
Laser welding technology is used extensively in the manufacturing business to cut and splice plates and other equipment. Inappropriately sized plates and equipment require cutting and splicing. At this time, professional and satisfactory laser welding technology is useful. Laser cutting method irradiates the material’s surface with a high-energy laser beam, causing the substance to melt, evaporate, or swiftly approach the ignition point, allowing for non-contact cutting. Laser cutting provides several advantages over traditional mechanical cutting processes, including quick speed, excellent precision, a tiny heat-affected zone, and minimal material deformation. Laser welding technology can be used to weld equipment and increase production efficiency and product quality in the manufacturing business, particularly in some steel plants. For example, in the process of laser cutting, focus position control technology can reduce the focus spot diameter by precisely adjusting the focal depth of the focusing lens, ensuring that the laser energy is highly concentrated and high-precision cutting is achieved; for thicker materials, pre-punching technology is employed. Before laser cutting, a small hole is pre-punched in the material by mechanical or laser methods so that the laser beam can accurately enter the material; during the process of laser cutting, the nozzle shape and airflow control technology are reasonably designed to ensure that the oxygen and the laser beam are fully mixed, improve the cutting efficiency, and at the same time, the molten material is ejected and blown out, reducing the heat-affected zone and material deformation. High-precision welding relies heavily on automation systems. Laser welding equipment that use machine vision systems and machine learning algorithms can monitor welding quality in real time and make automatic adjustments based on input to increase welding quality and efficiency. Welding settings and procedures vary depending on the material. High-precision welding equipment typically include a number of process parameter options to fulfill the needs of different materials.
Future Trends in Laser Welding
1. Intelligent Development
With the ongoing growth of intelligent manufacturing, the coupling of laser welding technology with robots and sensor technology will become more common. Robots can correctly conduct welding jobs, whereas sensors can continuously monitor various welding factors such as temperature, pressure, welding speed, and so on. By combining these technologies, the laser welding system can accomplish intelligent manufacturing, automatically modify welding parameters to suit various welding operations, and increase welding quality and efficiency. For example, in the automotive industry, intelligent laser welding robots may automatically alter welding pathways and settings based on the welding requirements of various models, resulting in efficient and accurate welding.
2. Green and Environmental Protection
Laser welding, being a green and environmentally friendly welding method, will gain popularity in the future. The laser welding technique is contact-free and pollution-free, and it produces no toxic fumes or smoke, meeting modern manufacturing’s environmental standards. As environmental rules become more rigorous, an increasing number of businesses will choose for laser welding technology to lessen their environmental impact. For example, in the sector of electronic production, laser welding can replace traditional welding procedures, reducing electronic waste generation and environmental contamination.
3. Various Applications
Laser welding will be used in a broader range of applications as technology advances. Laser welding can be utilized in the manufacturing of solar panels, wind turbine blades, and other new energy applications. Laser welding can be utilized in the manufacturing of sewage treatment equipment, rubbish incinerators, and other environmental protection applications. Laser welding can also be used for medical equipment, precision instruments, and other applications. For example, in the production of new energy cars, laser welding can produce efficient and precise welding of battery packs, hence boosting battery safety and durability.
4. Technological Innovation And Efficiency Enhancement
As laser technology advances, it is projected that lasers with more power, smaller size, and improved electro-optical conversion efficiency will emerge. These technological advancements will immediately increase the speed and quality of laser welding while lowering energy usage. For example, high-power fiber lasers will allow for faster welding speeds and deeper penetration depths, making them ideal for welding thick plate materials. Ultrafast lasers can be utilized for micro-nano welding and precision machining, improving welding accuracy and quality.
5. Extension of Application Fields
Laser welding technology will be extended to high-end industries such as new energy, aerospace, biomedicine, and precision manufacturing. In the realm of new energy, laser welding can be utilized to increase the performance and safety of power batteries. Laser welding can be used to make high-precision parts that fulfill the aerospace industry’s stringent product quality and performance standards. In the realm of biomedicine, laser welding can be used to verify the precision and quality of medical devices. For example, in the manufacturing of aircraft engines, laser welding may produce high-precision welding of high-temperature metals, improving engine performance and durability.
6. Market Demand Increase
As the global industrial industry transforms and upgrades, the demand for automated and intelligent welding equipment will increase. With rising labor costs and a shortage of experienced people, laser welding automation will become the preferred solution for the manufacturing industry. Laser welding automation equipment offers great efficiency, precision, and stability, which can improve production efficiency and product quality while lowering production costs. For example, in the automotive industry, laser welding automation equipment can achieve quick welding of car bodies, improve production efficiency, and lower production costs.
7. Integrating Automation And Intelligence
Laser welding technology will be seamlessly combined with robotics, artificial intelligence, the Internet of Things, and other technologies to create a highly automated and intelligent welding manufacturing line. This will enable adaptive control, real-time monitoring, and intelligent optimization of the welding process. For example, using artificial intelligence technology, the laser welding system can automatically detect the kind and thickness of welding materials, change welding parameters, and obtain the optimal welding effect. Laser welding equipment may be remotely monitored and managed using Internet of Things technology, which improves equipment usage and maintenance efficiency.
8. Customization And Personalized Production
Consumer desire for tailored items will propel laser welding technology toward customized production. Enterprises will be able to swiftly alter welding methods to meet client needs, resulting in small-batch and diverse manufacturing. For example, in the jewelry production industry, laser welding technology can build a variety of unique jewelry types based on customer preferences, meeting the need for personalized jewelry.
9. Development of Home Lasers
Domestic laser producers, such as Wuhan Ruike and Shenzhen JPT, will continue to invest in R&D to promote advances in domestic laser technology and expand production capacity. Domestic lasers will increasingly outperform international brands in terms of performance and dependability, while also lowering costs and increasing market competitiveness. For example, when domestic high-power fiber laser technology matures, their use in laser welding will become more widespread, giving great support for the growth of the home manufacturing industry.
10. Talent Development And Technological Innovation
As technology advances, the demand for professional talent will grow. Enterprises and research institutions will increase talent training and technical exchanges to encourage laser welding technology innovation. For example, by hosting laser welding technology training courses, seminars, and other events, more professional talent will be developed to boost laser welding technology innovation and advancement. At the same time, worldwide technological exchanges and collaboration will be strengthened, advanced laser welding technology and experience will be introduced, and the standard of domestic laser welding technology will be raised.
In Conclusion
From the perspective of the diversity of applicable materials, laser welding can handle both common metals and reflective materials with ease. In terms of micro welding and large weld welding, it demonstrates high flexibility and strong capabilities, meeting welding needs of different scales. The high repeatability, precise controllability and unparalleled speed of the results make laser welding important in large-scale production and industries with strict quality requirements. The characteristics of low heat input and few restrictions on component size further broaden its application range. The easy integration with motion products and the cost-effectiveness also make laser welding the first choice for many companies.
Laser welding technology plays an indispensable role in modern manufacturing. With the continuous advancement and innovation of technology, it will bring more opportunities and challenges to various fields and make greater contributions to promoting the development of the global manufacturing industry.
If you also want to own a laser handheld welding machine suitable for beginners, click to check it out.