Introduction
What are laser cutting machines?
A laser cutting machine is a device that employs a powerful laser beam to precisely cut workpieces.

Under the control of a computer, a laser beam focuses on a very small area of the workpiece surface, allowing the material to melt and evaporate, which is then blown away by high-pressure gas to complete the cutting process. Laser cutting machines are widely used in the manufacturing industry due to their fast speed,
With the development of technology, DIY laser cutters have become an affordable solution. Users can choose and create their own laser cutters, which not only lowers the entry barrier but also enables individuals and small companies to leverage the machines for innovation and production.
Overall, laser cutting machines play an important role in modern manufacturing due to their high precision, efficiency, and variety of applications. The invention of personal laser cutting equipment has opened up new options for laser cutting enthusiasts and small enterprises.
Affordable laser cutting devices have emerged as strong instruments for creativity and production.
How Do Laser Cutting Machines Work?
The laser cutting machine directs high-density power onto the workpiece’s surface, causing the surface temperature to rapidly rise to the melting and evaporation points, completing the cutting process.
During cutting, the CNC system directs the cutting head to follow the predetermined trajectory, while cutting gas is ejected from the nozzle to remove the molten material, resulting in cutting debris.
Laser cutters generate small heat-affected areas, thin silts, and high-quality cuts as a type of contactless cutting process.
What Are The Types Of Laser Cutting Machines?
Laser cutting machines can be classified into many varieties based on different criteria, including the type of laser, structure, cutting materials, laser power, and other factors. The precise categorisation criteria are as outlined below.
Classified By Laser Type:
- CO2 laser cutting machines: They excite electric currents to produce lasers, using CO2 gases as a laser medium. CO2 laser cutters can cut both metal and non-metal materials, such as acrylic, wood, and plastic. They have wavelengths of roughly 10.6 μm.
- Fiber laser cutting machines: The laser medium in these devices is made of optical fibres doped with rare earth elements. Diode pumping is the process used to create lasers. The primary applications of fibre laser cutters are in the cutting of metals, including carbon steel, stainless steel, and aluminium alloy. Fibre lasers have a wavelength of 1.06μm and can cut at a relatively high speed and electricity-light transmission.
- YAG laser cutting machine: Its laser medium is usually neodymium-doped yttrium aluminium garnet (Nd: YAG), and it operates using a solid-state laser source. This machine is best suited for processing thinner metal sheets because it is mostly used to cut metal products.
Classified by Structure:
- Gantry laser cutting machine: It is ideal for huge materials or heavy industry, the workpiece moves while the laser remains fixed during cutting.
- Cantilever laser cutting machine: This kind of cutter is ideal for small to medium-sized workpieces because the laser head is fixed at one end.
- Robotic arm laser cutting machine: Designed for intricate or three-dimensional cutting, this machine uses a robotic arm to cut lasers.
Classified By Cutting Materials And Uses:
- Metal laser cutting machines: Apply for cutting a wide range of metals, including brass, carbon steel, stainless steel, aluminium alloy, etc.
- Non-metal laser cutting machines: Apply for cutting non-metals like paper, plastic, and wood, etc.
Classified By Laser Power:
- Low-powered laser cutting machines: They are ideal for thin materials or cutting applications with minimal needs.
- Medium-powered laser cutting machines: They are ideal machines for cutting medium-thick materials because they strike a balance between cutting speed and equipment costs.
- High-Powered Laser Cutting Machines: They are suitable for heavy materials and can meet the needs of large batches of production.
Important Components of Fiber Laser Cutting Machine

- Laser Source: The laser source is the most important part of a laser cutting machine because it makes lasers that can cut through different types of material. A CO2 laser cutter uses CO2 gas, a fibre laser cutter uses doped fibre, and a crystal laser cutter uses YAG, YVO, and other laser gases.
- Control System: The control system is the laser cutting machine’s brain. It takes in the user’s cutting directions and patterns, controls the laser source’s output, and moves the motion system to make precise cuts. A CNC system and special software are part of the operating system.
- Motion System: It has servo motors, guide tracks, gearbox devices, and other parts that move the cutting head along the path that was planned. How well and how accurately the motion system works directly affects the quality and speed of the cutting.
- Cutting Bed: The laser cutting machine’s moving work area, or cutting bed, is where the piece of metal is put down and held in place. Many things go into deciding the size of the cutting bed, like the material’s size, weight, how stable it needs to be while it’s being cut, and so on.
To sum up, the type of laser cutting machine and its main parts decide how well it works, what it can be used for, and the quality of the cuts it makes. For this reason, getting the right machine and knowing how its parts work are very important for precise and high-quality cutting.
Project Planning
When planning to build your own DIY laser cutter, you should consider many factors, including clear needs, calculated budget, laser source and power, cutting area, and the size of the machine.

Figure out what you need and how much you can spend.
First, be clear about what you need to cut. That’s the first thing to do. The things you need to figure out are what kind of cloth you want to cut and how thick it is. It’s also important that the machine you want cuts accurately and quickly.
A reasonable budget range is set based on these needs. This range should include all the required parts, materials, and extra software or tools.
Pick a type of laser cutter (gantry, belt-driven, or rack-and-pinion).
Gantry, belt-driven, and rack-and-pinion laser cutters are the three main types of do-it-yourself laser cutters.
The gantry design structure is stable and good for cutting large areas. The belt drive system is cheaper, easier to set up, and good for light to medium precision work. The gear rack drive has better precision and speed, making it good for precise cutting.
Choose the right laser power and source
The laser source directly affects how well and how much it costs to cut. CO2 lasers, fibre lasers, and diode lasers are all common types of laser sources. Fibre laser cutters can cut metal, but CO2 laser cutters are better for cutting things that aren’t metal. You should think about laser power when picking a fibre source. The cutting speed and the thickness of the material that can be handled are better when the power is greater.
The main materials you want to cut and your cash should help you decide which laser power and source to use.
Think about the machine size and the cutting area.
The cutting area determines the machine’s size, which also affects where it can be stored and how much room it needs. So you need to know how big the cutting area is in order to pick the right machine. To be accurate, a laser source needs to be stronger when cutting areas that are bigger.
By following the steps above, you can plan and build your own laser cutting machine in a way that makes sense so that you can make creative things at home or in the workshop.
DIY Laser Cutter Step by Step
With the main DIY idea structure and strategy in place, let us begin the steps to making a laser cutter. I will go over the precise manufacturing process and the nuances involved.
Step 1: Frame Construction
- Build the frame
Use steel to construct a stable frame, ensure that all components are parallel and vertical, and leave room for the installation of components such as the mobile system and cutting bed. - Assemble the gantry or motion system
Install the Z-axis and Y-axis motion systems on the frame using belt or screw drive. Adjust belt tension or screw nut for smooth operation without jamming or stagnation. - Install the upper and lower structures of the laser head
Using a screw or ball screw for accurate Z-axis movement. - Install the cutting bed
Place the honeycomb cutting bed at the bottom of the frame to support the workpiece. The bed must be both horizontal and vertical to accommodate the laser head, and the height is adjustable.

Step 2: Laser and optical component settings.
- Install the laser source
Fix the CO2 laser tube and diode laser module to the frame. Heat dissipation and shockproofing are important for extending service life. Connect the high-voltage or drive energy, making sure the wires are properly connected and insulated. - Adjust mirror and lens
Install a reflector at the laser output port and adjust the angle to emit the laser beam vertically. Install the focussing lens on the cutting head and adjust the focal length to ensure that the laser beam is focused on the material’s surface. Continuous fine-tuning can optimise the optical path and increase cutting performance. - Connect water cooling (if applicable)
The CO2 laser tube comes with a water cooling system. Connect the water inlet and return pipes, check that the water connection is tight and closed, and make sure that the cooling water circulates smoothly and without leaks.
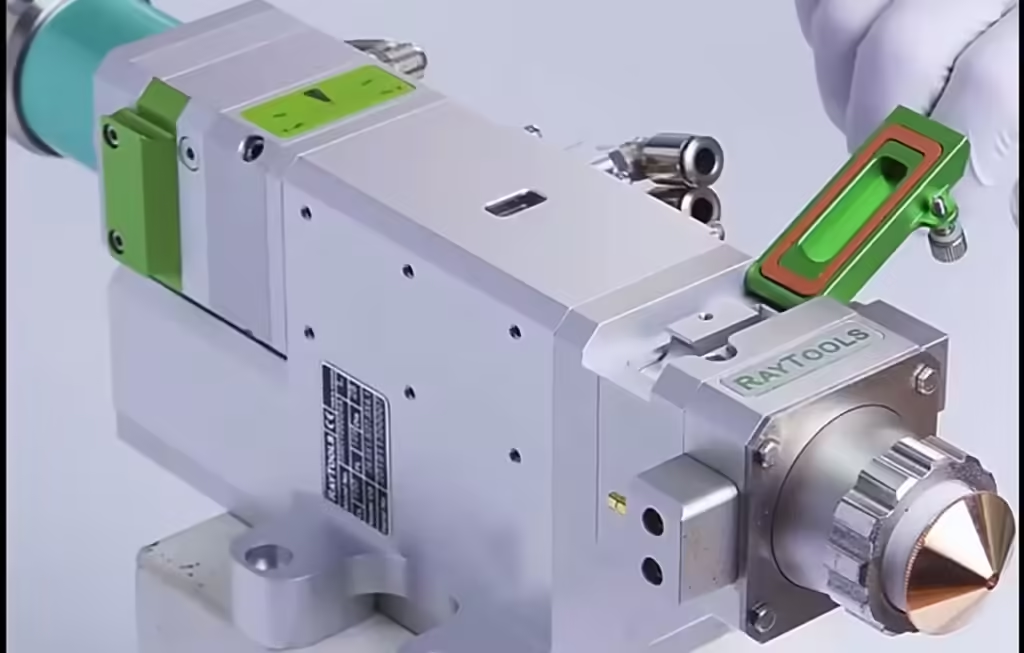
Step 3: Electronic parts and wiring
- Wiring for stepper motors and limit switches
The motor is wired on the X, Y, and Z axes to ensure a proper connection. To prevent laser head collisions, install limit switches at both ends of the motion axis and connect them to the control board. - Connect the laser control board, power supply, and driver
Choose the appropriate connection method based on the type. Check the line connection carefully to ensure that the signal is properly transmitted and that no other components are burned. - Configure power supply and emergency stop
Connect a suitable power supply to power the laser, control board, and motor. Equipped with an emergency stop switch to turn off the power in an emergency to ensure safety.
Step 4: Software Configuration
- Install and set up the control software
Choose compatible control software based on the type of control board. Adjust the laser power, speed, and cutting parameters in accordance with the software settings. - Calibrate the laser cutter
Adjust the position of the laser head and cutting bed for accurate focus. Run the calibration program to determine motion accuracy and repeatability in the X, Y, and Z directions. - Conduct a test cut
Prepare test materials like wood and acrylic and place them on the cutting bed.
Create a simple cutting pattern and send it to the laser cutter for testing. Both circles and squares are acceptable.
Evaluate the cutting results, then optimise the cutting parameters in preparation for actual cutting.

By following the steps and precautions I’ve outlined, I believe you’ll gain a better understanding of laser cutters as you learn about them. So, without further ado, let’s start building our own laser cutter together.
In Conclusion
The initial section of this article provides a comprehensive explanation of the definition of laser cutting machines, their operational principles, and their detailed classifications in order to facilitate your comprehension of the subsequent content.
The primary objective of this article is to examine the manufacturing process and the preparation of components for the production of laser cutting machines. I am of the opinion that reading my article will provide you with a more profound comprehension of the process of constructing a laser cutter.
We, Pendstar Laser, possess a wealth of scientific expertise in the field of laser cutting machines and employ a team of highly skilled operators. We specialise in the sale of laser cutting machines and machine components.
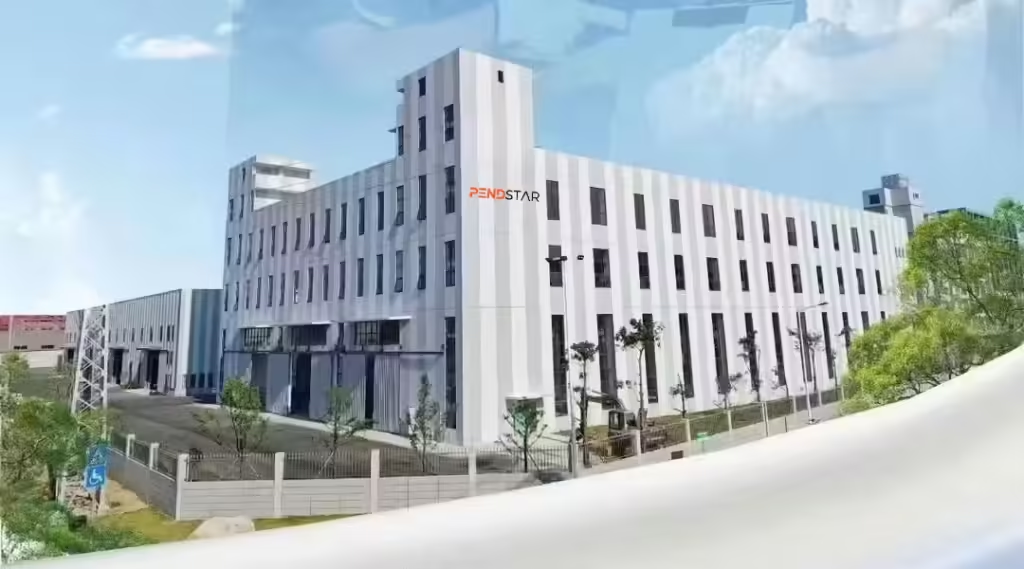
If you require components for the construction of your own laser cutting machine, you may consult our product page. Please do not hesitate to reach out to us if you have any additional enquiries.